Preserving the Lifespan of Your Foundry Induction Melting Furnace: Maintenance Tips and Tricks
October 19th, 2023
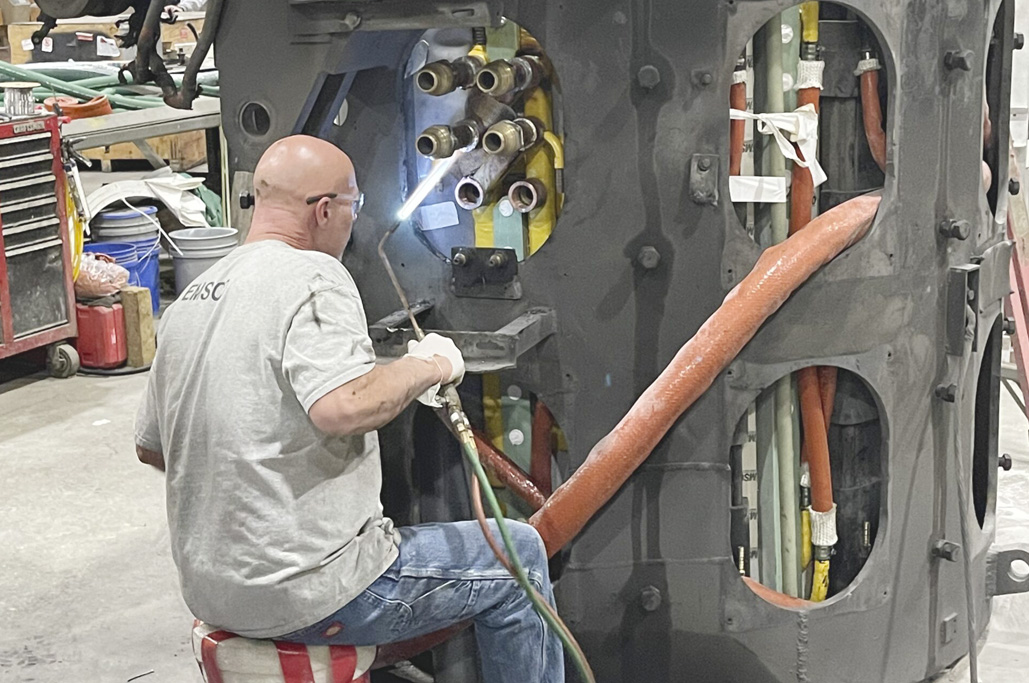
An induction melting furnace is an essential cornerstone in the bustling world of foundries, crafting raw elements into masterful metallic wonders. However, the key to unlocking its full potential and longevity lies in its operation and meticulous upkeep. Regular attention to maintenance can lead to heightened productivity, reduced operational costs, and an extended furnace lifespan. When equipped with the correct knowledge, you can preserve and enhance the performance of your foundry’s induction melting furnace, ensuring its role as the heart of your operations remains undiminished throughout its lifespan.
The Risks of Neglecting Induction Furnace Maintenance
Neglecting induction melting furnace maintenance in a foundry can result in grave operational and financial consequences. An induction furnace lacking regular care can consume excessive electricity, which increases costs. Accumulation of residues and contaminants can compromise the quality of melted metals, potentially producing subpar final products. If unchecked, wear and tear on integral components can disrupt seamless operations, precipitating unanticipated downtimes and hindering production schedules. Of even greater concern, an ill-maintained furnace can pose safety threats. Explosions, fires, or hazardous emissions may jeopardize the safety of foundry workers. Warranty voidance could also ensue from negligence, leaving foundries to shoulder heavy furnace rebuilds or replacement expenses. In essence, skimping on induction melting furnace maintenance not only undercuts operational efficiency but also imperils safety, product quality, and financial stability.
Routine Checks: The Backbone of Melting Furnace Longevity
Routine checks are indispensable in fortifying a foundry’s induction melting furnace for the long haul. These regular inspections ensure the induction furnace’s intricate mechanisms function at their prime, staving off undue strain on critical components. By diligently monitoring elements like furnace cleanliness, proper torque of furnace components, signs of moisture, excessive heat, and loose or broken parts, foundry personnel can intercept and make minor induction furnace repairs before they morph into major setbacks. Early identification of wear signs through these evaluations facilitates timely interventions, whether for foundry rebuilds or parts replacements. Such proactive practices dramatically mitigate the chances of unplanned downtimes, which could otherwise wreak havoc on production timelines and budgets.
With consistent evaluations of the critical elements: furnace cleanliness, routine torque of loose parts, monitoring for moisture and signs of overheated parts — potentially detrimental to the longevity of your induction melt furnace — remain in check. When graced with regular attention, an induction melting furnace not only operates at peak efficiency but also stands a greater chance of outlasting its expected lifespan, thereby delivering superior value to the foundry. These routine checks serve as the lifeline, ensuring a foundry’s melting furnace remains both effective and enduring.
Induction Melting Furnace Maintenance Guidelines
To properly maintain induction equipment, there are some foundry service guidelines that should be followed.
WARNING
Do not perform any maintenance on the system with power on. Following proper lockout/tagout procedures, place cabinet switch or circuit breaker off. Padlock or secure input power (circuit breaker switch) to off to prevent accidental live power onto the system. Be sure to discharge capacitors and turn off the circuit breaker.
Except for visual checks of the meters and lights on the outside of the VIP cabinet, a qualified maintenance person must perform all troubleshooting, maintenance, and repair. This qualified maintenance person must be able to recognize “shock hazards” and be trained in the safety precautions required to avoid possible injury or death.
If work needs to be performed on a tilted furnace, it is critical to secure the furnace in the tilted position with mechanical support. Reliance on hydraulics alone could lead to the furnace dropping without warning, causing injury or death to anyone trapped underneath.
1. Do not use any conductive hose. Conductive hose will cause arcing in the furnace coil and component loss in the power supply.
2. All hose clamps must be stainless steel. Both clamp band and worm gear must be stainless. Low-carbon steel clamps will inductively heat and burn the hose, causing a leak.
3. Do not substitute brass, bronze, or stainless hardware for ferrous hardware. Ferrous hardware will heat inductively, causing arcing and equipment failure.
4. All wood replacement coil supports or termination support blocks must be kiln-dried maple. Other materials will contain or absorb moisture, carbonize, and arc, which can result in coil or power supply failure.
5. All interlocks must be in working order. At no time should they be bypassed.
6. All SCR and diode devices must be replaced according to the procedures stipulated in the maintenance manual.
IF THESE PROCEDURES ARE NOT FOLLOWED, THE DEVICE WILL FAIL AND WEAKEN OTHER DEVICES. OF PARTICULAR IMPORTANCE IS TO ENSURE THE CENTERING ALIGNMENT PIN IS LOCATED IN THE HOLE OF THE DEVICE AND PROPER CLAMP PRESSURE IS APPLIED.
Foundry’s Induction Melting Furnace Maintenance Checklist
Daily Maintenance
- Check for and correct any water leakage at the furnace
- Check for and correct any hydraulic leaks
- Check for cleanliness around the furnace
- Check the operation of the ground leak detector
- Check refractory for damage
- Check lining for erosion
- Check spill pit
Monthly Maintenance
Ensure power is off and cannot be turned on while working on furnace coils.
You should remove your furnace’s inspection panels at least once a month to perform specific tasks and checks.
- Clean inside the shell if necessary
- Check the coil for signs of overheating or discoloration
- Inspect all water connections for signs of leaks
- Inspect wood blocks in the termination area and the wood coil supports for signs of burning or carbonization
- Check hydraulics
Replace the furnace panel covers. After replacing the furnace inspection panels, continue with additional checks.
- Check the hydraulic power supply
- Inspect the furnace lining for signs of deterioration, cracks, or metal penetration
- Inspect furnace leads for signs of external water jacket cracks or deterioration
- Check tie rods for tightness
- Inspect the furnace bus for signs of arcing or overheating. Check all bus hardware for loose connections and tighten
- Check flow switches for proper operation
The OEM (Original Equipment Manufacturer) recommends this checklist for routine maintenance. These daily and monthly reviews ensure the longevity, efficiency, and safety of a foundry’s induction melting furnace, helping foundries maintain consistent production quality and reduce downtime.
Professional Foundry Services: When and Why
Professional maintenance for your foundry’s induction melting furnace is pivotal, ensuring its optimal performance and extended lifespan. The intricate complexities of these induction furnaces often require expertise beyond routine checks, making the use of foundry service experts indispensable. At certain junctures, especially after prolonged use, induction furnace rebuilds become necessary. Such rebuilds, executed by specialists, can revitalize an aging induction melting furnace, enhancing its efficiency and restoring its former prowess. Moreover, professional foundry services guarantee a comprehensive examination of many induction furnace components. These foundry service experts, like the ones at EMSCO, employ advanced skills, ensuring that even minuscule irregularities do not escape their scrutiny. They also come equipped with the latest knowledge of induction melting furnace technologies, allowing them to recommend upgrades or modifications to meet evolving industry standards. Entrusting your induction furnace repair to professional hands not only ensures its seamless operation but also maximizes its productive life, safeguarding your foundry’s investment and reputation.
Recognizing the Warning Signs: When It’s Time for Repairs or Replacement
Recognizing the warning signs in your induction furnace can spell the difference between timely intervention and costly downtime. As the induction melting furnace ages, subtle indicators might hint at its declining efficiency or potential malfunction. Unusual noises, inconsistent temperature regulation, or a sudden spike in operational costs can serve as red flags. Additionally, if the quality of molten metals starts to waver, the induction furnace might need immediate attention. In situations where these symptoms persist or escalate, consulting foundry service professionals becomes essential. The experienced professionals at EMSCO can provide an in-depth analysis, determining whether repairs can restore the induction furnace’s functionality with induction furnace rebuilds or if a complete replacement remains the most viable solution. Staying vigilant to these signs ensures that necessary measures are taken promptly, protecting your equipment’s productivity and longevity.
When it comes to metallurgy, a foundry’s induction melting furnace stands as a linchpin, turning raw metals into molten marvels. Consistent maintenance emerges as the non-negotiable mantra to ensure this cornerstone of metalwork continues to function at its height. Proper care, guided by expert tips and tricks, does not merely prolong the induction furnace’s life but also elevates its performance, yielding top-notch results. By heeding early warning signs and prioritizing professional foundry services, foundries can ward off unexpected hitches and costly disruptions, like major induction furnace repairs. Moreover, by investing time and resources in routine checks and timely interventions, the induction melting furnace remains a reliable ally, enhancing productivity and ensuring a superior quality of molten metal. The combination of meticulous care, foundry service expertise, and proactive measures secures the exceptional performance of a foundry’s induction melting furnace, solidifying its position as the central force in metal transformation.
From repairing/rebuilding induction melting furnaces and coils, to installing complete melt systems, EMSCO has generations of experience providing foundry services for your furnace.
Contact us today for more information about our furnace rebuilds, table mount furnace repairs, melt deck designs, and other foundry services!